Eversub: Polish company ROV in the offshore sector
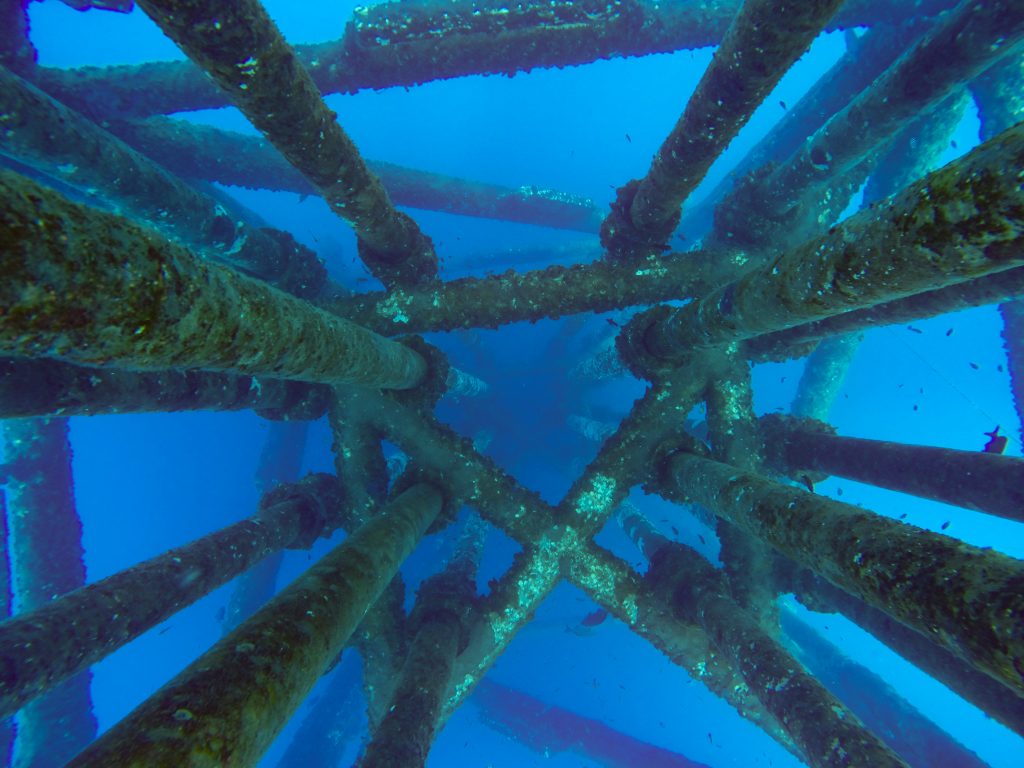
In recent years we have observed a rapid development of underwater robotics. The main reason for this is the desire to increase the level of safety and eliminate the human risk factor in underwater work.
The work performed by divers is associated with logistical problems. They must have a diving base with a system and qualified personnel.
The best solution to increase safety and minimize costs is the use of Remotely Operated Vehicle (ROV).
Using them by the owners and operators of vessels / maritime and inland infrastructure reduces the risk, costs, and at the same time speeds up the time of execution of orders. Therefore, all newly designed and implemented subsea installations are specially designed for remote controlled underwater robots.
For several months now, the Polish company Eversub has been offering its activities in the field of underwater works with the help of ROV, providing its services, among others, to the marine mining and renewable energy sectors. For this purpose, it uses remotely controlled underwater robots with a depth of up to 1000 metres. Thus, the robots are able to perform their tasks at the maximum depth of the Baltic Sea and the North Sea.
The robot used for underwater work has a modular structure and can be easily configured for the job. It can be equipped with a manipulator arm, a wide range of sonars and sensors of any kind.
It is also equipped with a high-resolution camera and lighting. The image from it can be transmitted live to any place in the world, and recorded for further analysis. Eversub robots also use a laser imaging system. In this way, the currently collected measurement data of the structure or the bottom enable 3D modeling in real time. This is the latest method of modeling time differences and the inspection is more accurate than traditional sonar inspections. Using this method allows you to model damage and corrosion perfectly, predict the life of the structure and solve problems efficiently.
In case of limited visibility, Eversub offers its customers the use of a 3D echoscope or various types of sonar. The robot can also be equipped with a cathodic protection measurement system as well as an ultrasonic thickness gauge system. The robot equipped in this way gives a wide range of applications in the maritime sector. From simple visual inspections to advanced inspections of oil rigs, wind farms, ship hulls and offshore installations of all kinds. Eversub also uses fiber optics on one of its robots instead of standard cable. In this way, the configured robot is able to flow into wrecks, caves, mines or any kind of confined spaces with limited manoeuvrability.
It is worth mentioning that this kind of solution was used by Robert Ballard during the exploration of the interior of RMS Titanic. In the maritime sector it is used, among others, for checking the interior of wrecks, ship tanks or even sea pipelines.
Eversub company uses the latest scientific and technological approaches, constantly looking for new methods of assessment and monitoring of the underwater environment.
www.eversub.com
info@eversub.com